Polyethylene Catalyst Technologies
Polyethylene resins produced using catalysts in low-pressure reactors include linear low-density polyethylene (LLDPE) and high-density PE (HDPE). Low-density PE (LDPE) uses a different, high-pressure process that does not use these catalysts but may involve organic peroxide initiators. Conventional catalysts used in LLDPE and HDPE manufacturing processes include precipitated or supported Ziegler-Natta (ZN) catalysts, or chrome-based catalysts on silica. In the 1990s, single-site metallocene catalysts with a transition metal, such as titanium or zirconium, sandwiched between one or more cyclopentadienyl rings, came into use for making polyolefins. More recently, advanced ZN catalysts have been developed. Catalysts are one crucial part of the process, and the type of reactor (eg, gas-phase reactor, slurry-loop reactor) is another. Most licensors are promoting multiple reactors to optimize the processability and mechanical properties of PEs. Each end-use application requires specific PE resin attributes, microstructure, and processability, which are often satisfied by only the right combination of a specific PE process and a suitable catalyst. Low-pressure reactor technology is ripe for innovation to satisfy many of the process/product requirements and improvements.
Market Drivers in the Polyethylene Catalyst Market
Catalysts for low-pressure polyethylene processes were initially supplied by the technology licensors, but as patents have expired, third-party producers have entered the market. For example, with the expiration of key metallocene patents in 2011, the technology held by a few is becoming more widespread via licensing and cross-licensing catalyst agreements. Each catalyst supplier (inventor or third-party) has a specific catalyst portfolio. The expansion of the polyethylene industry with new capacity being built in the US as well as other areas, is driving demand for catalysts. Expansions in some regions of the world and slowdown in other regions will create a shift in catalyst demand and global PE capacity. Catalyst selection determines the properties of the polymer; producers choose a catalyst based on their target market and the properties that the end-use application requires. The exhibit below shows the value chain at a high-level. Catalyst selection determines the properties of the polymer; producers choose a catalyst based on their target market and the properties that the end-use application requires.
Exhibit 1. Polyolefins value chain
Polyethylene Catalyst Market Assessment
ADI Chemical Market Resources (ADI CMR) has conducted a strategic analysis that covers all major developments in the industry including changing market dynamics, technology trends, evolving industry structure and strategic alliances, and the current and expected competitive landscape. Market forecasts are presented by region and application. This study will assess the relative position of each catalyst supplier in this niche, but dynamic and high-margin market. Another goal of this study is to review the catalyst needs per region and per process technology. The report is based on thorough analysis of the industry through a wide range of methods, including published information, patent searches, ADI CMR proprietary projects, and interviews with catalyst suppliers and resin producers. The report will particularly benefit polyethylene producers, and catalyst suppliers, as well as individual end-users, entrepreneurs, and organizations attempting to understand these complex issues and capture future growth in the marketplace. ADI CMR has specialized reports on the global markets for the polyolefin product families, including metallocene-catalyzed elastomers and plastomers, MDPE/HDPE, and PP.
Table of Contents
Click here to view the table of contents for this report.
Prospectus
Please fill this form and check your email for a link to download the prospectus. For a custom report on a topic of your choice or an updated version of an existing report, please contact us at +1 (281) 506-8234 or info@adi-cmr.com.
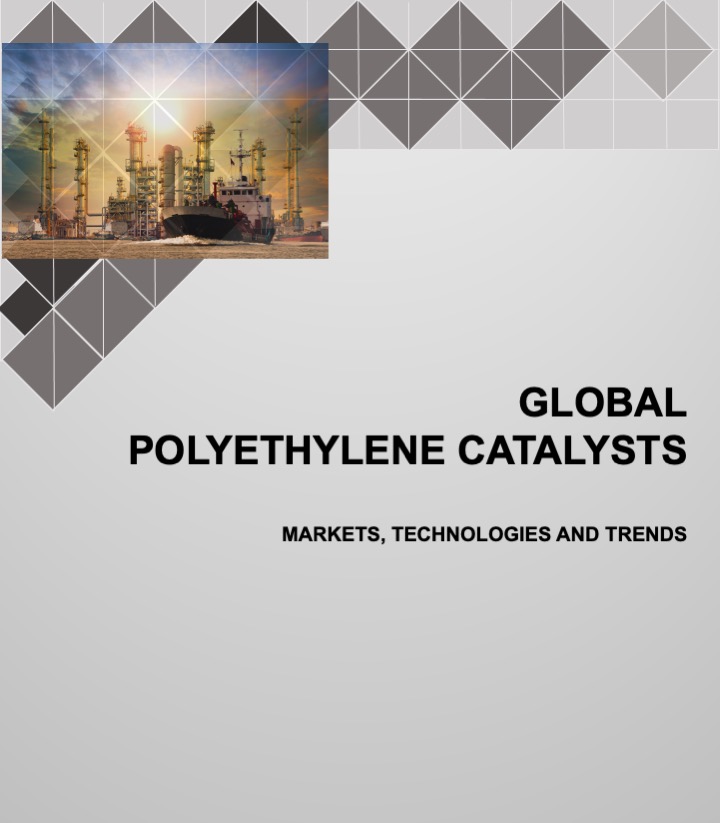